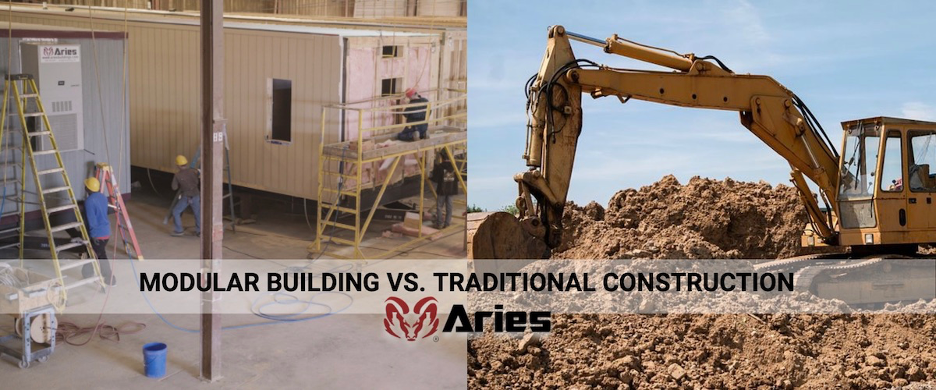
In traditional construction, raw materials are taken to a job site and everything is put together right on top of the foundation. On the other hand, with modular construction, instead of taking the raw materials to be built on-site, modules are built in a factory, and then delivered and completed on the foundation. Sometimes known as pre-fabrication, modular building has been around for hundreds of years, but recent technology has made modular construction more versatile than ever. Today’s modules all contain electrical connections, plumbing, and interior
amenities already set up. Furthermore, the modules can be stand alone or linked together to make large and more complex buildings.
Why do businesses choose modular?
As a construction method, modular construction offers many benefits derived from its assembly line and factory-controlled conditions. Primordially, it counteracts the biggest challenges to traditional construction.
The traditional construction industry “holds the dubious honor of having the lowest productivity gains of any industry […]. In America, astonishingly, [productivity] has plunged by half since the late 1960s,” according to The Economist.
Weather delays, coordination breakdowns, and workplace accidents all contribute to the lackluster performance of many traditional construction companies.
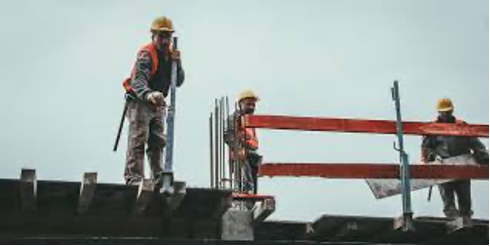
Many of these obstacles are intrinsic characteristics of the industry. For example, many of the jobsites do not have addresses, making delivery of the raw materials cumbersome. Worker productivity typically suffers in extreme weather conditions, where the workers are exposed to the elements. Furthermore, for long stretches of time, the on-site workers and overseers are often left to their own devices, meaning that if they need extra information or a problem arises, they could be sitting around waiting for answers from off-site decision makers.
The following list elaborates how modular perfectly combats these deficiencies.
Benefits of modular construction
ü Speed:
· The foundation of the building is prepared while the building is being constructed in the factory, compressing the overall building timeline.
· Building in a factory speeds up the process of acquiring building codes.
· Assembly line manufacturing reduces construction time of the building itself.
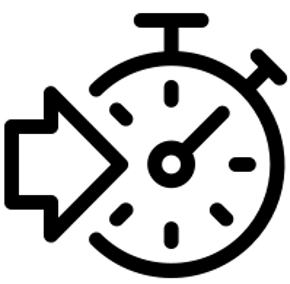
- Safety and less disruption:
There are many places – i.e. schools, hospitals, retirement homes, shopping centers – whose daily activities come into direct conflict with the chaos generated on a construction site. For these institutions, having a modular building reduces the risk of accidents. In addition, the speed of setting up the modular buildings means that there is less noise, clutter, and traffic to disrupt their operations.
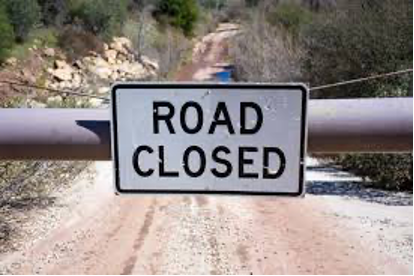
- Affordability:
Because of the efficiency of factories, modular buildings usually cost less than their traditional counterparts.Here
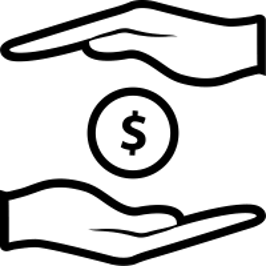
- Environmentally friendly:
Another benefit of factory-controlled conditions used in modular building is that material waste is greatly reduced when compared to traditional construction.
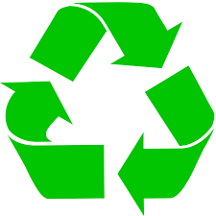
Are there any drawbacks to modular construction?
- Limited design options:
Often, the most cited “con” to modular construction, which are the limits to design options, are quickly becoming a thing of the past. Today’s modular buildings are becoming more customizable and versatile than ever. However, for the most creative projects, modular building can still be limiting. Most noticeably they are limited in the types of materials that can be used in the construction.
- Limited size of the rooms:
While the buildings themselves can be almost infinitely large, the individual rooms may sometimes be limited by the transportation capacity of trucks and roads.
- Financing:
Clients should look for companies that offer financing options, as many banks finance brick and mortar buildings differently than modular buildings.
- Perception:
The public retains a negative conception about the quality of modular buildings. This notion continues despite evidence to the contrary, with the factory-controlled buildings, designed for transportation, often are sturdier than traditionally built structures. With so many spectacular modular buildings going up, everything from skyscrapers to luxury hotels, the perception of modular buildings is also on the rise.
ABOUT ARIES – Aries has offices and operates in all regions across the U.S., including the Northeast, the Mid-Atlantic, the Southeast, the Midwest, South Central, the Southwest, the Pacific Northwest, and Canada. For this reason, Aries features its modular short- and long-term housing in several locations across North America. Aries sells prefabricated office buildings to be used as construction offices, portable school classrooms, mobile hospitals, workforce housing at oil pipeline sites, storage containers, and for disaster recovery relief, but we’d love to help you buy one for any purpose at all! We offer full turnkey solutions with exceptional customer service and robust financing options. We pride ourselves on combining product quality, design expertise, technical and financial innovation, and strategy that has already established us a first choice to customers. Become a customer today! Visit Aries: www.ariesbuildings.com, or call (U.S.) 1-888-598-8869. You can also contact us via our website, or request a quote here.