It’s no secret what 3D printing is anymore. Amazing jumps in technology have allowed us to create, innovate, and possibly do it at a faster pace and lower cost than traditional production with 3D printing. Let’s imagine for a minute what modular building is: building pieces off-site and constructing the pieces together on-site. We also have heard it called ‘prefab’ construction (more popular in residential building communities).
When it comes to traditional construction, you pick your site, you stack your lumber, steel, and materials on site, and you have a building. As you build, you have inspectors that make sure you are passing codes, zoning, and somewhere a general contractor is tracking cost, inventory, labor, theft (happens more than you think), and on top of that is trying to determine the weather patterns to make sure his crew doesn’t get rained out.
Modular construction literally lets you build the walls (and other pieces) at a separate location to specification, there’s no worry about theft, and the pieces are built to code and zoning regulations and inspectors approve multiple pieces at a time. You literally have an inventory of modular structures that can be transported off the shelf like a prefabricated building store.
It’s obvious to see that there’s benefit to modular over traditional construction (and FEMA agrees) and they are just as sturdy; if not more sturdy (ask HUD) than traditional building. In fact, modular buildings are more common than you could imagine.
But what about 3D printing?
Investors and builders everywhere have stars in their eyes as they imagine lower material usage, lower labor costs, and less expensive construction costs in general: what a beautiful profit!
And yes, there are benefits as pointed out by UC Berkely research. Imagine having giant 3D printer warehouses that can now build at the warehouse and be shipped off to site much like the modular building process? Currently, printers only manufacture out of plastic, resin, ceramics, and certain metals. However, the printers are quite costly, and the circuit boards and ability to program these printers is quite timely. The next problem is the size of these printers: which is not small. We also still have yet to see a 3D printer complete a project with the speed and accuracy of modular building. Beyond that, large 3D printers cannot finish a project (meaning the aesthetic finished look) and needs another step to have a project ‘completed’. And something that is even a step beyond THAT notion, are the tech files behind 3D printing: will there be intellectual property rights on a digital file that protects a manufacturer in a certain ‘wall type’ or similar? While 3D printing has its roots in creating sustainable and cheap building, do we now have a marketplace flaw that will inhibit production costs?
Now let’s throw in another factor of the final process of building and construction: things like electric, plumbing, windows, doors, joints, finishes, all which require significant labor and time: and are all inter-dependent on where you’re building. Los Angeles has different building codes for fire, earthquake, and wind than Houston, which needs less earthquake assurances than say; hurricane sturdiness (Aries prides itself on blast resistant buildings).
For now, the amount of work beyond printing is just as much, if not more time strenuous and labor intensive as building modular. While there are great strides in 3D printing construction (check out what they’re doing in Singapore) there are many unknown factors. It is something that Aries may consider in the future as 3D printing evolves as the standard and quality of printing improves.
Aries Building Systems can help you achieve your next construction project, whether it’s custom-built or one of our existing models. View our modular inventory here; https://ariesbuildings.com/inventory-list/
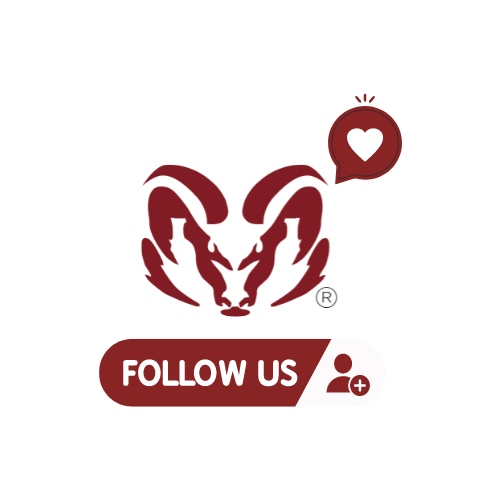